Efficiencies of Modular Fabrication in Commercial Construction
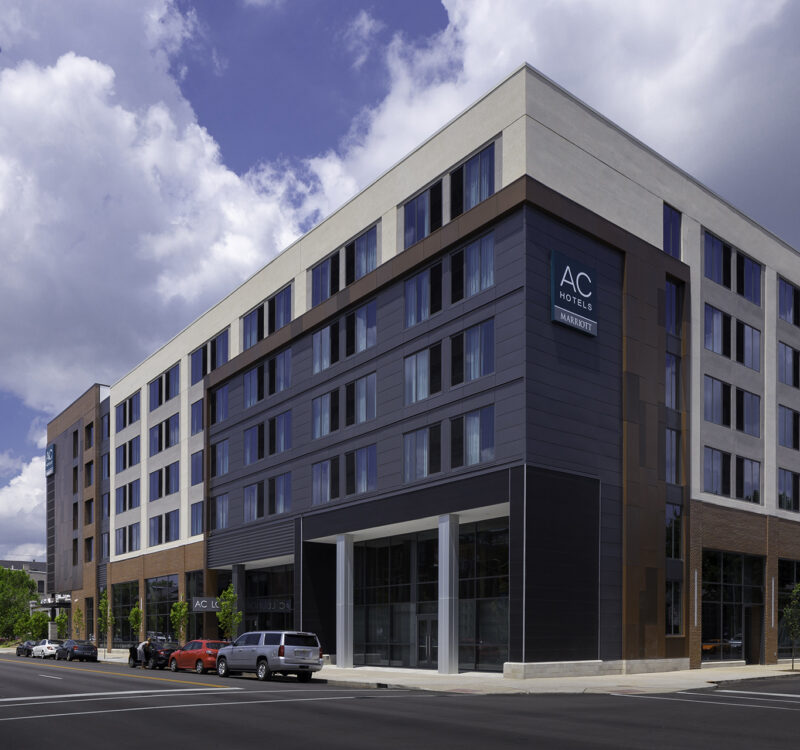
Guestrooms are a critical part of any hospitality establishment. Often, guests judge the hotel’s quality not by the amenities offered in the lobby, the equipment provided in the exercise room, or the speed of the internet connection but by the quality of the guest’s experience within their room. Fragrant shampoos, fresh linens, and large-scale televisions are of no comfort if the craftsmanship of the vanity or the furniture within the room is not up to par with the guest’s expectations.
Enter Pre-fabrication
Champion Home Builders, based in the U.S., has been a manufacturing company specializing in prefabricated homes and commercial buildings since 1953. The concept for the product is simple; create a product that can be efficiently manufactured to a high standard under the controlled conditions of a factory floor and installed on a job site like an appliance within its own box. Popularized by efficiency and the skyrocketing costs of skilled job site labor, the concept of prefabricated building components has succeeded in speeding up construction schedules and thereby saving money on projects.
This concept, however, had been slow to catch on in the United States, especially in high-end hotels and commercial buildings. Champion Home Builders is leading the way by simplifying one of the biggest headaches in hospitality construction, consistency within the guestroom.
Most recently, Meyers+Associates has worked with Champion Home Builders for the AC Hotel Downtown Louisville. Champion was chosen to reduce construction time, labor costs and provide a higher quality end product consistent from room to room.
Diagram of the Champion units
Design Process
Prefabricated guestrooms and modular construction help to mitigate the amount of on-site coordination required by the general contractor and subcontractors. The efficiency comes into play in the amount of time needed to install and finish the prefabricated guestroom and corridor versus building a traditional stick-built guestroom floor.
Champion units can be set at a rate of approximately 10-12 double-loaded corridor units per day with a setting crew. A punch list is not required since all prefabricated units undergo inspections at the factory and are shipped sealed to the job site. The guestroom interior is 90% finished when it arrives on the job site, and the last 10% is simply putting up any wall-hanging items and final checks to make sure everything arrived safely to the final location.
Conceptual rendering to understand the modular process once guests arrive on-site and set in their final location. The general contractor will complete the exterior as a “skin” applied to the finish surface of the modular guestrooms.
For the highest success rate, modular vendors are brought into the design process early to add the most significant benefit to the design of the project look, construction, and schedule sequence. Working with the owner and the architect, the vendor can design the most efficient layout for the modules and create on-site coordination. Because of their relationship with many of the leading hotel chains in the United States, Champion is familiar with franchise standards. Having the pre-manufactured vendor incorporated into the design team early ensures proper coordination of the guestroom unit with the building’s structural, mechanical, electrical, and plumbing systems. Additionally, this assists the hotel owner, architect, and contractor to ensure franchise standards are stringently adhered to even for high-end hotels.
Early in the project, the project team decided the lower lobby floors would be traditionally built on-site, essentially creating a flat “table” at the second-floor level to maximize the use of modular construction. The modules are then placed on top of the podium level and stacked on top of each other to create four guestroom floors and 156 total units. On-site development of the first two floors was able to continue construction without interfering with the modular stacking of the guestroom floors.
(left to right) Crane lifting the units into place; exterior of the building showing the units in place and corridor left exposed; and the corridor as the general contractor would see it to create the hookups.
Drawing Coordination Process
The owner, architect, and hotel brand worked to decide on a design and configuration with the efficiencies following the modular vendor for the best utilization of prefabricated units. Adjustments to the drawing documents were made to accommodate the different types of construction and sequencing of coordination in the field. Our documents create a clear designation between the two parties to better help the coordination effort between the modular vendor and the general contractor by utilizing a gray hatch for elements provided by the modular contractor. By implementing this style, the contractor clearly understood what was needed from his team, and the distinguishing of roles was essential in coordinating the efforts of all trades.
Champion Home Builders worked with the architect, general contractor, structural, and MEP consultants to make sure all phases of the project went seamlessly and forecast any potential items with the construction team. While the site work was beginning, the factory was well on its way to producing and packaging finished guestrooms in a separate facility, decreasing the overall schedule.
One of the main items during the coordination effort was regarding the corridor. Produced by the modular vendor and left unfinished, the guestroom units are stacked, and the general contractor comes through to create the hookups and coordinate through the floors to create a working system. There is no longer a need for the contractor to enter the guestroom since it is almost finished.
October 5, 2017 Final modules are set into place
October 5, 2017 Final modules are set into place
March 15, 2018 On-going exterior materials applied to modules
April 25, 2018 Building completed in time for April 28th opening
On-Site Construction Process
The pre-manufactured guestrooms are manufactured at the onset of the job and stored in a warehouse after production. Once the building has reached a particular completion stage, including the podium level, the units are shipped to the job site on trucks and placed in the back of the site until they are ready for installation.
Once delivered to the job site, the units were installed by being lifted onto the podium by crane and stacked to create each floor adjacent to the previously set one. The units are delivered in plastic wrap to protect them from damage until they are ready for final placement and connections.
156 guestroom units were placed in under three weeks, completely furnished within the room. The unit is shipped with the exterior sheathing, window, and louvers for the vtac units, essentially ready for the outer skin to be applied. Once the modules are in place, the general contractor can begin to make connections within the corridor since the corridor is completely exposed when the modules are produced and allows the building inspectors to have full access to the corridor connections for inspection. Once inspections and connections are complete, the corridor is ready to be finished and closed.
At Meyers+Associates, we continue to explore the advantages of using pre-manufactured components in buildings that require consistent, high-quality craftsmanship across many units, such as in hospitality and housing projects. We recognize the benefits pre-manufacturing can bring to a project and invite the opportunity to be on the leading edge of this part of the building industry. Client response has been positive, and they appreciate the consistency of craftsmanship and savings associated with a reduced project schedule pre-manufactured building components can provide. Further distinguishing the AC Hotel Louisville and its construction is its LEED Gold Certification. The project also received the 2020 National Association of Home Buildings: Awards for Excellence: Commercial Project and the 2018 Modular Building Design Award of Distinction.